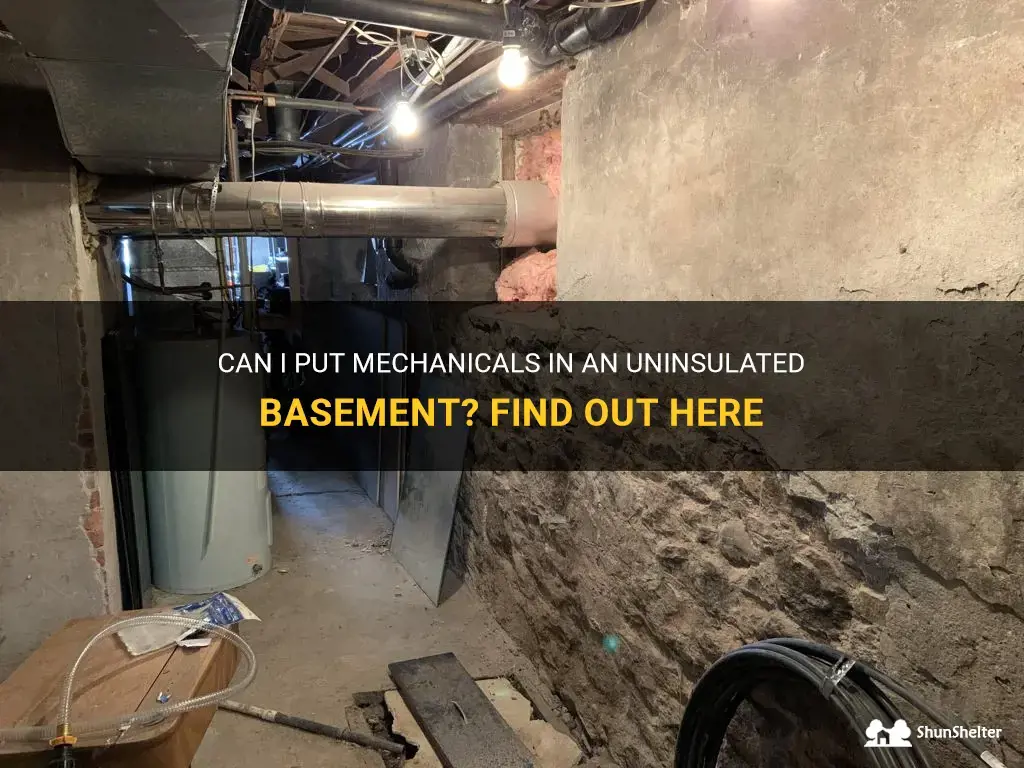
Putting mechanicals in an uninsulated basement can give rise to a combination of challenges and advantages. On one hand, the lack of insulation might expose these systems to extreme temperatures, risking potential damage. On the other hand, the basement's openness allows for easy access and ventilation, making maintenance and repairs more convenient. Whether you're considering setting up your mechanicals in an uninsulated basement for practicality or necessity, it's important to carefully evaluate the potential benefits and drawbacks to ensure optimal performance and longevity.
What You'll Learn
- What are the potential risks or drawbacks of putting mechanical systems in an uninsulated basement?
- Are there any specific building codes or regulations that dictate whether or not mechanicals can be placed in an uninsulated basement?
- What are some potential energy efficiency concerns related to placing mechanical systems in an uninsulated basement?
- Can insulation be added to an uninsulated basement in order to improve the performance and efficiency of mechanical systems?
- Are there any specific considerations or precautions that should be taken when installing mechanical systems in an uninsulated basement to minimize potential issues or complications?
What are the potential risks or drawbacks of putting mechanical systems in an uninsulated basement?

Uninsulated basements are a common feature in many homes, and can provide a versatile space for housing mechanical systems such as HVAC units, water heaters, and other equipment. However, there are several potential risks and drawbacks associated with putting mechanical systems in an uninsulated basement.
One of the primary concerns with an uninsulated basement is the risk of condensation and moisture buildup. Basements are typically cooler than the rest of the house, and if warm air from the mechanical systems comes into contact with the cool walls and floors, it can result in condensation. This can lead to mold and mildew growth, which can be detrimental to both the mechanical systems and the overall indoor air quality of the home.
In addition to the potential for mold and mildew, an uninsulated basement can also result in energy inefficiency. Without insulation, the mechanical systems will have to work harder to maintain desired temperatures, leading to increased energy consumption and higher utility bills. This can be particularly relevant for HVAC units, which may struggle to heat or cool the home effectively if located in an uninsulated basement.
Another drawback of putting mechanical systems in an uninsulated basement is the potential for damage from extreme temperatures. In regions with very cold winters, uninsulated basements can become frigid, putting strain on the mechanical systems and potentially causing them to fail. Similarly, in hot climates, the lack of insulation can lead to excessive heat buildup in the basement, which can negatively affect the performance and longevity of the equipment.
Additionally, an uninsulated basement may not provide adequate protection against noise and vibrations. Mechanical systems can be noisy, and without insulation to absorb or dampen the sound, the noise can easily travel to other parts of the house. This can be particularly problematic if the basement is used as a living space or if there are bedrooms or quiet areas nearby.
To mitigate these risks and drawbacks, it is important to consider insulating the basement and providing proper ventilation. Insulation can help regulate temperature and reduce condensation, making the space more comfortable and less prone to mold and mildew growth. Proper ventilation, such as exhaust fans or a dehumidifier, can also help remove moisture and improve indoor air quality.
In conclusion, while an uninsulated basement may seem like a convenient location for mechanical systems, there are several potential risks and drawbacks that should be considered. From condensation and mold growth to energy inefficiency and potential damage from extreme temperatures, the lack of insulation can have significant implications for the performance and longevity of the equipment. Taking steps to insulate and properly ventilate the basement can help mitigate these risks and ensure the optimal functioning of the mechanical systems.
Exploring the Feasibility of 15 Amp Circuits in Basement Bathrooms
You may want to see also
Are there any specific building codes or regulations that dictate whether or not mechanicals can be placed in an uninsulated basement?

When it comes to building codes and regulations, there are typically guidelines in place to ensure that homes and buildings are constructed in a safe and efficient manner. While the specific regulations may vary depending on the location and jurisdiction, there are generally no specific codes that dictate whether or not mechanicals can be placed in an uninsulated basement.
However, it is important to note that building codes often require certain standards to be met when it comes to the installation and use of mechanicals. For example, the National Fuel Gas Code (NFPA 54) provides guidelines for the installation of gas equipment, including furnaces and water heaters, to ensure the safety of occupants. These guidelines may include requirements for proper venting, clearance from combustible materials, and access for maintenance.
In addition to the NFPA 54, the International Mechanical Code (IMC) provides regulations for the installation, operation, and maintenance of mechanical systems, including heating, ventilation, and air conditioning (HVAC) systems. The IMC addresses issues such as equipment location, access for maintenance, and clearance requirements. While the IMC does not specifically address insulation, it does provide guidelines for the safe and efficient operation of mechanical systems.
So, while there may not be specific codes or regulations that dictate whether or not mechanicals can be placed in an uninsulated basement, it is important to ensure that any mechanical systems in the basement are installed and operated in accordance with applicable codes and regulations. This includes ensuring that proper clearances are maintained, proper venting is provided, and that the equipment is easily accessible for maintenance.
In terms of the benefits of insulating a basement that houses mechanical systems, there are several factors to consider. Insulation can help to improve energy efficiency by reducing heat loss in the winter and heat gain in the summer. This can lead to lower energy bills and a more comfortable living environment. Insulation can also help to reduce moisture and condensation in the basement, which can help to prevent mold and mildew issues. Finally, insulation can provide added soundproofing, reducing noise transmission from the mechanical systems.
In conclusion, while there may not be specific building codes or regulations that dictate whether or not mechanicals can be placed in an uninsulated basement, it is important to ensure that any mechanical systems are installed and operated in accordance with applicable codes and regulations. Insulating the basement can provide several benefits, including improved energy efficiency, reduced moisture issues, and added soundproofing. Consult with a local building inspector or a qualified professional to ensure that your basement and mechanical systems meet all necessary requirements.
How to Deal with Fungus Gnats in Your Basement
You may want to see also
What are some potential energy efficiency concerns related to placing mechanical systems in an uninsulated basement?

When it comes to energy efficiency, the location and insulation of mechanical systems play a crucial role. Placing mechanical systems in an uninsulated basement can lead to several energy efficiency concerns. In this article, we will explore some of these concerns and discuss potential solutions.
Heat Loss: An uninsulated basement can lead to significant heat loss. As the mechanical systems generate heat, it can escape through the walls and floor of the basement, resulting in energy waste. This can put a strain on the heating system and increase energy consumption.
Solution: Insulating the basement walls and floor can help reduce heat loss. Insulation materials such as foam boards, spray foam, or batt insulation can be used to create a thermal barrier. This will help retain the heat generated by the mechanical systems and reduce energy wastage.
Condensation: An uninsulated basement can be prone to condensation issues. When warm air from the mechanical systems comes into contact with the cold surfaces of the basement walls and floor, it can cause moisture to condense. This can lead to mold growth, structural damage, and reduced energy efficiency.
Solution: Installing insulation can help prevent condensation by creating a thermal barrier. Additionally, proper ventilation should be in place to remove excess moisture from the basement. This can be achieved through the use of exhaust fans or a dehumidifier.
Energy Overconsumption: Placing mechanical systems in an uninsulated basement can result in increased energy consumption. The systems will need to work harder to compensate for the heat loss and maintain the desired temperature, leading to higher energy costs.
Solution: Insulating the basement will help improve the energy efficiency of the mechanical systems. By reducing heat loss, the systems will operate more efficiently, leading to lower energy consumption and cost savings.
Comfort Issues: An uninsulated basement can make the living spaces above it uncomfortable. Cold floors, drafty rooms, and inconsistent temperatures can affect the overall comfort of the building.
Solution: Insulating the basement will help stabilize the temperature and create a more comfortable living environment. It will also help prevent drafts and cold floors, making the space more enjoyable to occupy.
Environmental Impact: Placing mechanical systems in an uninsulated basement can have a negative environmental impact. The increased energy consumption will lead to higher carbon emissions and contribute to climate change.
Solution: Insulating the basement and reducing energy consumption will help lower carbon emissions. This can be achieved through a combination of insulation upgrades and the use of high-efficiency mechanical systems.
In conclusion, placing mechanical systems in an uninsulated basement can lead to various energy efficiency concerns. By properly insulating the basement and addressing these concerns, it is possible to improve energy efficiency, increase comfort, and reduce environmental impact. It is recommended to consult with a professional to determine the best insulation and ventilation options for your specific situation.
Installing a Natural Gas Generator in Your Basement: What You Need to Know
You may want to see also
Can insulation be added to an uninsulated basement in order to improve the performance and efficiency of mechanical systems?

Adding insulation to an uninsulated basement can significantly improve the performance and efficiency of mechanical systems in a building. Uninsulated basements are prone to heat loss and infiltration, which can greatly impact the overall energy consumption and comfort of a space. By insulating the basement, building owners can reduce energy costs, enhance the performance of heating and cooling systems, and create a more comfortable indoor environment.
Insulating a basement can be accomplished using various materials, including spray foam insulation, rigid foam insulation, fiberglass batts, or mineral wool insulation. The choice of insulation material will depend on factors such as the budget, desired R-value, and moisture resistance.
Before proceeding with the insulation installation, it is crucial to assess the existing condition of the basement and address any moisture issues. Basements are often more susceptible to moisture problems compared to the rest of the building due to their below-grade position. Conducting a thorough inspection and implementing proper waterproofing measures is a necessary step to prevent future issues such as mold growth or structural damage.
Once moisture concerns are addressed, it is time to select the appropriate insulation material. The insulation should have a high R-value to provide efficient thermal resistance. The R-value measures an insulation's ability to resist heat transfer, with higher values indicating better performance. The recommended R-value for basement insulation will depend on the climate zone and the specific requirements of the building.
Spray foam insulation is a popular choice for basement insulation due to its high R-value and ability to seal air leaks effectively. It can be applied directly to the basement walls or ceilings, providing both insulation and an air barrier. Spray foam insulation also has the advantage of preventing moisture intrusion and reducing the risk of mold growth.
Rigid foam insulation boards are another viable option for basement insulation. They can be easily installed on basement walls, providing excellent thermal resistance and moisture resistance. Rigid foam insulation boards are available in different thicknesses, allowing building owners to achieve the desired R-value.
Fiberglass batts and mineral wool insulation are more traditional options for basement insulation. They can be installed between studs in framed walls or the ceiling joists. These insulation materials are cost-effective and offer good thermal performance. However, they may require additional measures to address air leakage, such as using caulking or sealing tapes.
In addition to insulating the walls and ceilings, it is important to consider insulating the basement floor. Uninsulated basement floors can become a significant source of heat loss. Insulation materials such as rigid foam boards or spray foam can be installed on the floor before finishing it with a suitable flooring material.
By insulating an uninsulated basement, the performance and efficiency of mechanical systems can be enhanced. The insulation reduces heat loss and infiltration, enabling heating and cooling systems to operate more efficiently. This, in turn, can lead to energy savings and lower utility bills. Insulation also helps create a more comfortable indoor environment by reducing drafts and cold spots.
In conclusion, adding insulation to an uninsulated basement is a valuable investment for improving the performance and efficiency of mechanical systems. Proper insulation materials and installation techniques should be chosen based on factors such as moisture resistance, R-value requirements, and budget constraints. By insulating the basement walls, ceilings, and floors, building owners can enjoy energy savings, enhanced comfort, and a more sustainable building.
Tips for Drying Marijuana: Can You Hang it in the Basement?
You may want to see also
Are there any specific considerations or precautions that should be taken when installing mechanical systems in an uninsulated basement to minimize potential issues or complications?

When installing mechanical systems in an uninsulated basement, there are several considerations and precautions that should be taken to minimize potential issues and complications. By following these guidelines, homeowners can ensure the longevity and efficiency of their mechanical systems.
One important consideration is insulation. While the basement may be uninsulated, it is still recommended to insulate the areas surrounding the mechanical systems. This helps prevent heat loss and condensation, which can lead to moisture buildup and potential damage to the equipment. Insulating the walls and pipes can also help improve energy efficiency and reduce utility costs.
Furthermore, it is crucial to properly ventilate the basement to prevent the buildup of moisture and improve air quality. Mechanical systems generate heat and require proper airflow to dissipate it. Without sufficient ventilation, the basement can become humid, leading to mold growth and other issues. Installing vents or fans can help promote airflow and prevent moisture buildup.
In addition to insulation and ventilation, it is essential to consider the location of the mechanical systems within the basement. Placing them in an area that is easily accessible for maintenance and repair is crucial. It is also important to ensure that the systems are positioned away from potential water sources, such as sump pumps or basement windows, to minimize the risk of water damage.
When installing mechanical systems, it is necessary to follow the manufacturer's instructions and guidelines. This includes proper sizing, wiring, and any specific installation requirements. Failure to adhere to these guidelines can result in malfunctioning systems or voided warranties.
Lastly, regular maintenance is crucial to ensure the optimal performance of mechanical systems in an uninsulated basement. This includes regular filter replacements, cleaning, and inspections. It is recommended to consult with a professional technician to schedule routine maintenance and address any potential issues before they escalate.
To illustrate these considerations and precautions, let's take the example of installing a furnace in an uninsulated basement. Firstly, it is important to insulate the walls surrounding the furnace to prevent heat loss. Additionally, insulating the pipes connected to the furnace can help prevent condensation and potential damage.
Secondly, proper ventilation is essential. Installing vents or fans near the furnace can help dissipate heat and prevent the buildup of moisture. This is especially important for gas furnaces, as they produce combustion byproducts that need to be safely vented outside.
Next, the location of the furnace should be carefully chosen to allow for easy access and maintenance. Placing it away from potential water sources, such as a basement window or sump pump, can help minimize the risk of water damage.
During the installation process, following the manufacturer's instructions is crucial. This includes proper sizing, electrical wiring, and any specific installation requirements. Failure to follow these guidelines can result in improper functioning or potential safety hazards.
Lastly, regular maintenance and inspections are essential to ensure the efficient and safe operation of the furnace. This includes cleaning or replacing filters, checking for any leaks or malfunctions, and scheduling professional maintenance visits.
In conclusion, when installing mechanical systems in an uninsulated basement, there are several considerations and precautions that should be taken to minimize potential issues and complications. These include insulation, ventilation, proper location, adherence to manufacturer's guidelines, and regular maintenance. By following these guidelines, homeowners can ensure the longevity and efficiency of their mechanical systems.
Growing a Beautiful Garden in Your Basement: Tips and Tricks
You may want to see also
Frequently asked questions
Yes, it is possible to install mechanicals in an uninsulated basement. However, it is important to consider the impact of the uninsulated space on the performance and efficiency of the mechanical systems. An uninsulated basement can result in heat loss, which can put additional strain on heating equipment and increase energy costs. It is recommended to insulate the basement to create a more energy-efficient environment for the mechanical systems.
Insulating the basement before installing mechanicals offers several benefits. Firstly, it helps to create a more comfortable and consistent temperature in the basement, which improves the performance of the mechanical systems. Insulation also helps to reduce heat loss, which can lower energy costs and increase the efficiency of heating equipment. Additionally, insulating the basement can provide a barrier against moisture, helping to prevent potential damage to the mechanical systems.
Yes, it is possible to retrofit insulation in an existing uninsulated basement with mechanical systems already in place. However, this can be a more complex and challenging task compared to insulating a basement before installing mechanicals. The process may involve insulating around and between the mechanical systems, ensuring proper ventilation and clearances, and addressing any potential fire safety considerations. It is recommended to consult with a professional contractor or insulation specialist to ensure the proper insulation installation in an existing basement with mechanicals.